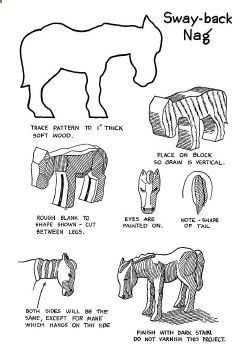
There are several factors to be aware of when shopping for an oar carver knife. When purchasing a knife for carving, size, sharpness as well as stag bone and lamination are all important factors to consider. This article will help you choose the best knife for your needs. After reading this article, you'll have an idea of what to look for when purchasing your new oar carving knife.
Size
The Oar Carver series of carving pocket knives is a classic and epitome of this craft. There are three sizes in the current lineup. Version 2 is larger, with a thinner blade. Version 3 features a thicker edge and a wider gap. These are some tips to help you choose the right size.
Sharpness
Sharpness is a key aspect of any oar carving knife. You should keep your knife's edge sharp. Your knife will begin to show signs of wear like chips, dullness and nicks. Luckily, it is relatively easy to gauge the sharpness of an oar carving knife by observing the edge. A magic marker will help you match the angles of each knife's blade to its center.
To test the sharpness or a oar carving knife, you can cut a piece out of basswood and cross it across its end grain. The blade should cut through the wood with no drag marks or ripples. A smooth cut is like cutting a baby's bottom without leaving any marks. If you see any of these marks on the blade, it might not be sharp enough to use for carving. It is important to regularly check the sharpness a oar-carving knife.
Laminated blades
The Oar Carver series, created by Ross Oar, a world-renowned knifemaker, is a classic example for the carving pocketknife. There are three versions currently: Versions 1, 2 & 3. Each version differs from the other. For example, Version 2 features a wider difference between the two blades. It also has thinner edges. For more information, see the Oar Carver blade guide.
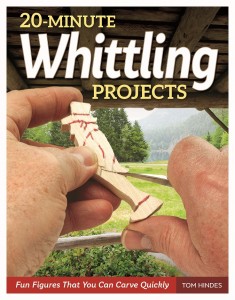
Mora makes two versions of the 106 and 120. The Mora knife has a longer blade made from laminated steel. Both knives are simple and have an oval handle. They also come with a snap sheath. Another model, the Mora Frost 122 has a laminated steel blade and a 61 Rockwell high hardness. This knife is perfect for carving. The blade is also sharp and long-lasting.
Origins
The oar carving knife was created in Japan from ancient times. The handle is 4 1/2 inches long and the blade is solid hardwood. The oar is a long, flat knife with a flat point. The knife's shaft is 53 inches in long. The handle is carved with a narrow circle while the blade and shaft have been separated by a thin wood section.
Although the oar is considered to be the oldest known tool for carving, its history is far more extensive. The oar was originally designed to be used by riverine and coastal people. Because it was easy to recognize and widely used, Admiralty chose the emblem oar. The oar might have had other meanings, however. These are just a few of its origins. If you are interested in learning more about the history and evolution of knife-making, they are also worth looking at.
FAQ
How long does a piece take to finish?
It depends on the type of wood you choose, the complexity of the design, and the amount of finishing you apply. Hardwoods are more difficult to maintain than softwoods. Hardwoods also tend to be more expensive than softwoods. However, they are stronger and more resistant to moisture. The typical time taken to finish a piece furniture takes anywhere from one to three month.
What tools work best for me?
It helps to reflect on your needs and preferences before you shop for tools. Do you prefer metal or plastic handles What size nails and screws do you usually use? Would you rather use hand tools than power tools?
Which material would you recommend for woodworking lessons?
Start with softwood like pine, poplar and ash. Once you feel comfortable with these two, move on to hardwood.
Is it easy to start a woodworking business?
Starting your own woodworking business isn't easy. There are lots of legal requirements and regulations that you'll need to follow. But, this doesn't mean you need to go through all of the trouble of setting up your business. Many people join already-established businesses. You will only have to pay membership fees, taxes, and other charges.
How much money will I need to get started?
Because every project is unique, there aren't exact numbers. These factors will help you get an estimate of how much money is needed.
-
Material cost
-
Tools and equipment
-
Time spent on the Project
-
Your hourly rate
-
What is your expectation for profit?
-
Hire help
For those just beginning, it may be a good idea to start small with simple items like boxes and picture frames. As you gain experience, you'll be able to tackle more complex projects.
Statistics
- Most woodworkers agree that lumber moisture needs to be under 10% for building furniture. (woodandshop.com)
- The best-paid 10 percent make $76,000, while the lowest-paid 10 percent make $34,000. (zippia.com)
- Overall employment of woodworkers is projected to grow 8 percent from 2020 to 2030, about as fast as the average for all occupations. (bls.gov)
- Woodworkers on the lower end of that spectrum, the bottom 10% to be exact, make roughly $24,000 a year, while the top 10% makes $108,000. (zippia.com)
External Links
How To
How to make wooden joints
This tutorial will show how to join 2 pieces of wood together. We will be using the "pocket-hole joint", which involves drilling holes in wood and then gluing them together. This works well if the wood is straight and smooth. Try dowel joinery instead if your wood doesn't look straight. Here are the steps
-
Drill Pocket Hole Joints. To start, measure and mark where you want to put the pocket hole joint. You will then drill 3/4" deep holes through each piece of wood with a jigsaw, handheld drilling machine, or hand-held drill.
-
Sand Smooth. Sanding the wood's edges will ensure that the joint doesn't split.
-
Glue Together. Apply glue on both sides of the wooden plank. Let it sit for about 5 minutes before clamping the pieces together.
-
Attach the Pieces together. After the glue has dried thoroughly, secure the pieces so that they are flush.
-
Trim Joinery. Trim any excess wood surrounding the joint once the glue has dried completely.
Be sure to leave enough space between each piece so that they can be turned inside-out.