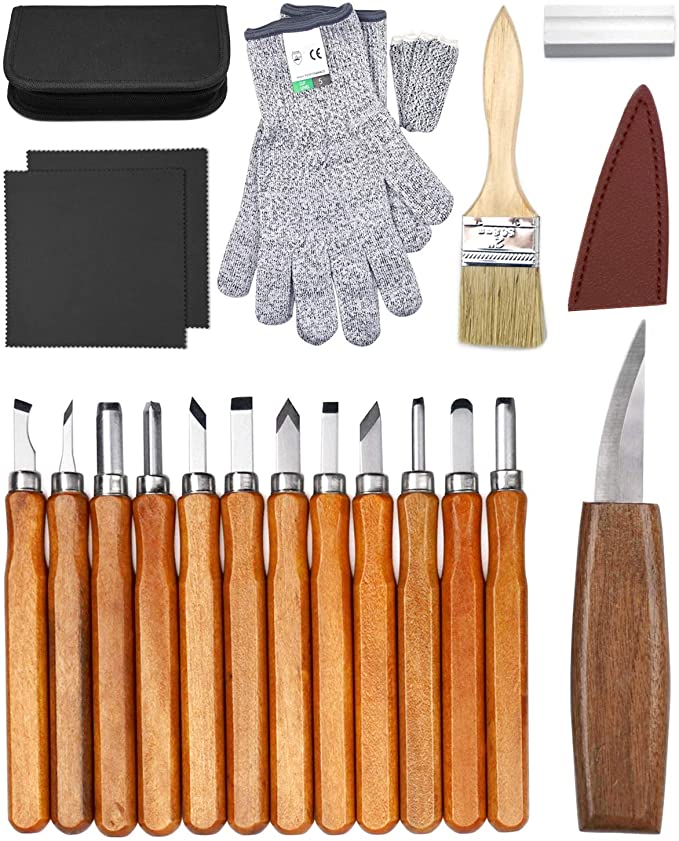
Select a piece of wood to begin carving a face out of wood. Make the necessary cuts. Follow along with the expert as he guides you through the steps. This will allow you to create a more realistic face by making the cuts in the wood. It is important to create a lifelike facial expression by adjusting the position of the noses in the wood. For a realistic finish, color dyes and shellac can be used in addition to the face outline.
Hardwoods
The type of wood used to carve a face in wood must be considered before you begin carving. Hardwoods are a class of trees with broad leaves that grow in a variety of climate zones. Hardwoods are suitable for various purposes due to their density, strength, appearance and versatility. Hardwoods can be more cost-effective than softwoods but are durable and fire-resistant.
If you're new to wood carving, you may want to consider using softwood, such as basswood or butternut. These woods can be easier to work in and are a great choice for beginners. However, you should remember that softer woods cannot hold the same quality and finish as hardwoods. Try different types of wood before you settle for one.
Softwoods
When carving a face from wood, the first step is to choose the right softwood. Softwoods can be more difficult to carve because they often have more knots. They can also be more fragile if you use long strokes. Beginning carvers will cut small pieces of timber, decreasing detail. While it's not a major problem, this is something to be aware.
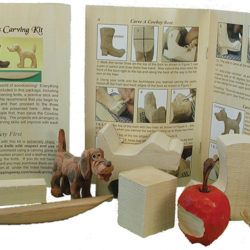
Some hardwoods can be more difficult than others. Aspen and butternut are the easiest hardwoods to work with. For this reason, it is best to use knives with a steeper bevel. Softwoods are also easier to work with than hardwoods, so you can carve them either along or across the grain. The quality and finish of your product will depend on what wood you use.
Colored Dyes
For wood carvings that are vibrant and detailed, you can use colored dyes. These dyes are available in a variety colors that can be mixed with water or alcohol to create unique colours. Use colored dyes that are mixed with shellac to lighten woods. After applying dyes, ventilate your work area and clean your brushes with denatured alcohol. You can also use paste wax. Excessive glossiness can distract you from your work. Use 0000 steel wool to remove excess glossiness.
There are many types of wood dyes that can be used and they are easy to apply. Wood dyes will work with all topcoats. They are also easy to apply. They solve common finishing challenges. They can be mixed and applied in a variety of primary colors. You can also mix and match them to your liking. They can also be combined to create unique colors.
Shellac
Shellac should be available before you apply it to your wood carvings. It is possible to buy a container of shellac but using a brush is the best method to apply it. Generally, a two-pound cut will do. This is because the shellac will gradually build up and will reduce brush marks. Also, it's better to buy a thicker cut than a thinner one, because shellac is very water-thin. You can make your own pads from cotton lumps the size of golf balls and lint-free cloth. After that, dip the tip end of your brush in the shellac.
Shellac can add color and highlight grain. Shellac is available as a variety colors. This allows you to mix and match different shades of resin to create your own blends. You can darken the shade with extra coats of lac. Shellac is not like other wood finishes. It won't become yellowed or cloudy over time. It will also last longer, so you can make more faces. This is possible with any type of wood carving project.
Gouges
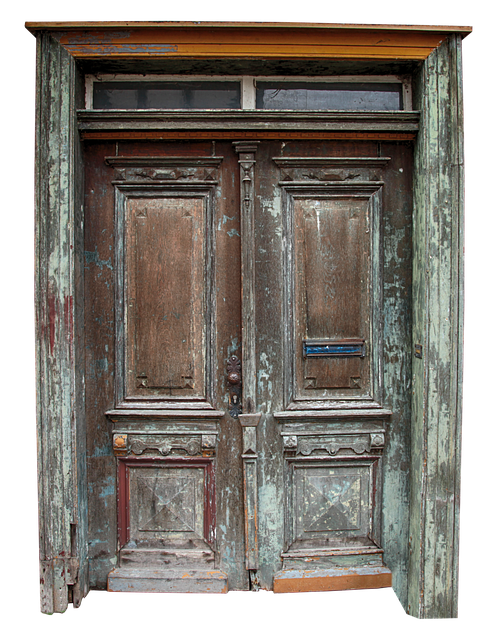
You can find a wide variety of sizes and shapes in gouges. The straight and the palm gouges types are the most commonly used. Straight gouges can only be held with one hand. Palm gouges, on the other hand, have shorter shafts. The shorter handles make hand held carving easier. Palm gouges are also called veiners and are ideal for carving faces in wood. Here are a few things to consider before you start carving.
First, it is important to understand how to select the correct gouge. The gouge you choose must be capable of creating a shallow, v-shaped groove. It is important to have a sharp edge, small sweep and a very small tool. Gouges are often categorized according to their size. A 3/10 gouge will make the same-size cut as a 5/10 gouge. The scoop between the edges will get deeper and the sweep will become more curled as the first number goes up. A gouge with a small sweep will be able to carve a shallow v-shaped profile.
FAQ
Do you have any suggestions for starting a woodworking shop?
It is hard work to start a woodworking company. It's worth it if you're passionate and willing to work hard. You might even enjoy running your own business.
You should remember that unexpected issues may occur when you launch a new venture. You may run out of money suddenly. Maybe customers won't be willing to pay what you want. These situations are necessary for survival.
Set up a separate account in your bank for your business. This will ensure that you always know how much money has come in.
How much will it cost to get started?
Because every project is unique, there aren't exact numbers. Consider these factors if you need to estimate the amount of money that you will require.
-
Materials cost
-
Tools and equipment
-
Time spent on the Project
-
The hourly rate
-
How much profit do you expect to earn
-
Whether you plan to hire help
For those just beginning, it may be a good idea to start small with simple items like boxes and picture frames. You'll become more proficient as you get experience.
What is the difference between a hobbyist woodworker and a professional woodworker.
Hobbyists like making things with wood. Professionals focus more on quality. Hobbyists tend to take pride and share their creations with family and friends. Before they start working on a project, professionals will spend hours researching the designs. They will pay attention to every detail, from selecting the best materials to finishing the project perfectly.
How do I calculate woodworking prices
When calculating the costs of any project, it is important to keep them as low and affordable as possible. Make sure you're getting the best prices on materials. It is also important to consider the costs of other factors, such time, skill, and experience. You can find an estimate of the cost of different woodwork projects in our guide to common DIY tasks.
What tools are best to begin with when I become a woodworker
Woodworking is an art. It requires patience. It takes time to master all the tools and techniques involved in woodworking.
There are many options for woodworking equipment today. Some people prefer to use power tools while others prefer manual tools.
You have the freedom to choose what tool you want, but it is important that you select the right tool for your job. If you don't have any experience, you may consider starting with a basic set of hand tools.
Another option is to learn how to use a router, which is used for cutting intricate shapes into wood. These can be found at most hardware shops.
How can I determine which tools are most suitable for me?
It helps to reflect on your needs and preferences before you shop for tools. Are you more comfortable with plastic or metal handles? What size are you most comfortable using for screws and nails? Do you prefer hand tools over power tools?
Statistics
- Most woodworkers agree that lumber moisture needs to be under 10% for building furniture. (woodandshop.com)
- The U.S. Bureau of Labor Statistics (BLS) estimates that the number of jobs for woodworkers will decline by 4% between 2019 and 2029. (indeed.com)
- Average lumber prices rose about 600 percent between April 2020 and May 2021. (familyhandyman.com)
- In 2014, there were just over 237,000 jobs for all woodworkers, with other wood product manufacturing employing 23 percent; wood kitchen cabinets and countertop manufacturing employing 21 percent. (theartcareerproject.com)
External Links
How To
How to join wood with no nails
Woodworking is a popular hobby. Woodworking is a relaxing hobby that allows you to use your hands to create useful things from wood. You may need to join two pieces without the use of nails. This article will explain how to do this so that your woodwork projects stay beautiful.
First, remove any sharp edges from the wood pieces before you join them. You don't want to leave sharp corners that could cause problems later on down the road. Now it's time to start glueing your boards together.
You should only glue one side of hardwood. For softwoods like cedar and pine, glue should be applied to both sides. After applying the glue, press the boards firmly until they are completely stuck together. Make sure you let the glue dry before moving on to the next step.
Once you've glued your boards together you will need to drill holes in the joints to accommodate screws. You can choose the type of screw to determine the size of your holes. If you plan to use a 1/2 inch wood screw, drill a hole at least 3/4 inches in depth.
After drilling the holes, you can drive the screws into your board's backside. Be careful not to hit the front surface of the board, or else you'll ruin the finish. Try to not hit the ends of the screws when driving the screws. This will prevent splitting the wood's end grain.
After your project is completed, you will need to protect it from the weather. You can either cover the entire furniture or just the top. You want it to last years, so you can use any product. Oil-based varnishes are, among others, polyurethanes shellac, laquer, and other oil-based products.
You can find these products at most home improvement stores. It is important to ensure that you purchase the correct product for the job. Also, remember that some finishes are toxic and should never be used indoors. Protective gear should always be worn when handling these finishes.