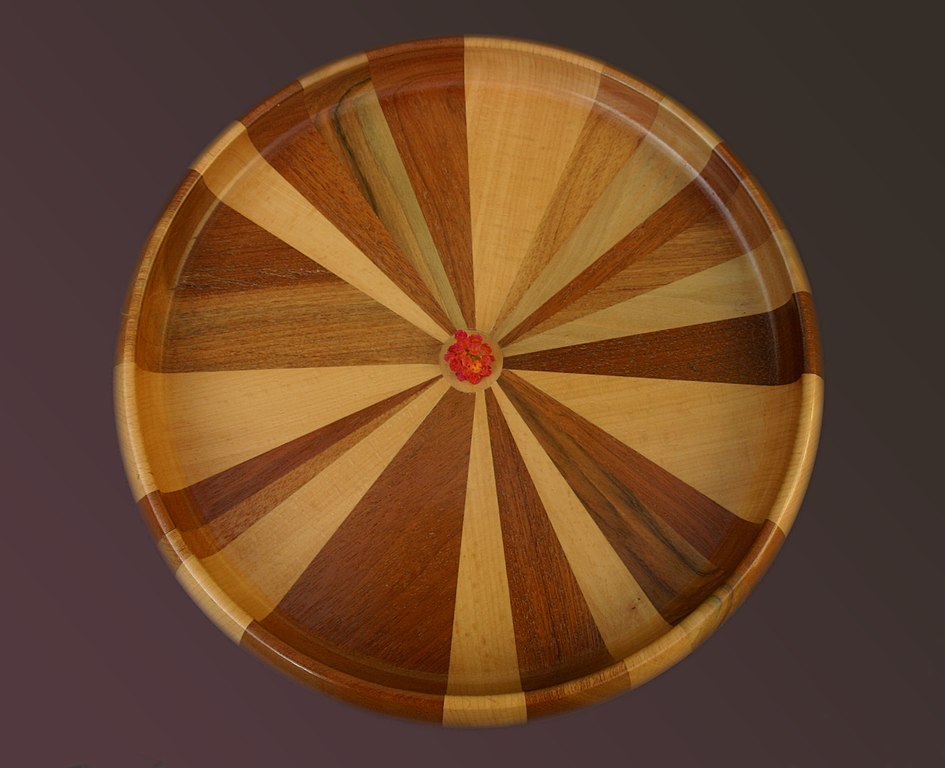
There are many different types of turning tools available. Some tools made from Carbide. Others are made with HSS, Skew or both. To maximize the cutting power of a turning tool, it should be properly sharpened. It can be frustrating for new turners to sharpen their tools. Many vendors offer tools with removable carbide inserts to make things easier. However, many experienced turners recommend using traditional tools instead, because they give you a better cutting surface on the wood, are more versatile in terms of types of cuts, and cost less in the long run.
Carbide
It can be extremely helpful to have several types of Carbide turning tools when working on a wood project. You have the option of a Savannah Large Carbide Turning Tool, or a smaller one. The Savannah Large Carbide Turning tool is perfect for wood turners with all skill levels. The Savannah comes with a rotatable cutterhead that makes it easier to maintain the tool's sharpness. This tool is also made of solid carbide which will remain sharper longer than traditional tools made from steel.
While the features of different carbide turners tools are similar, their uses can be quite different. These carbide inserts are commonly referred to by the term "square-edged" tool. The square-edged carbide inserts will be the most effective in fastening and removing heavy materials, while the slightly rounded carbide inserts will provide a smooth finish to the final product.
HSS
Diamond hones can be used to sharpen HSS turning tools. HSS tools can be sharpened quickly with diamond hones. Preferences can vary when sharpening HSS and carbide scrapers. Some turners prefer the small burrs that are created by grinding wheels over hones. These preferences depend on the type and style of your tools.
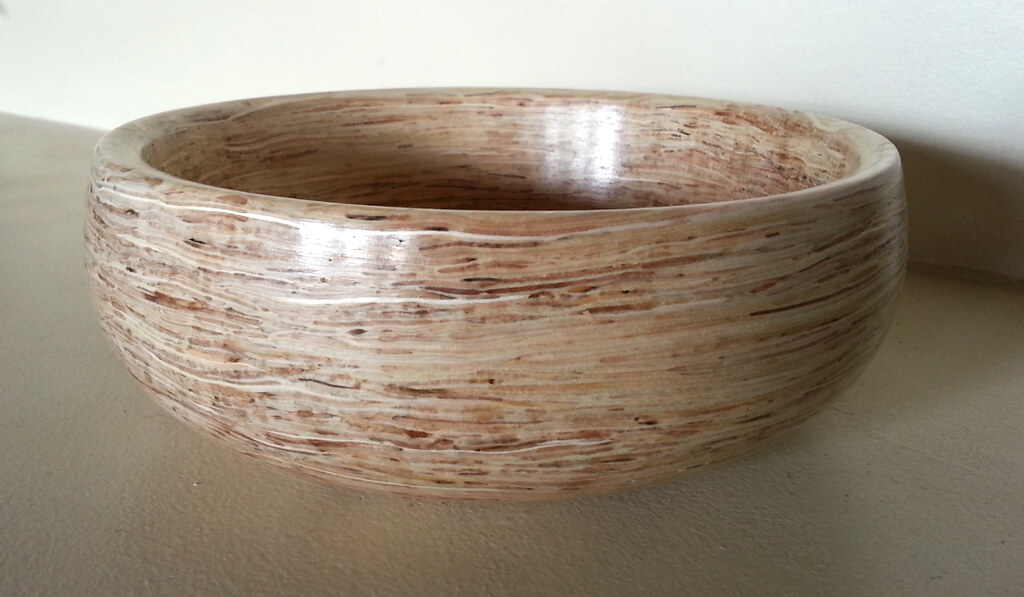
Carbide tools can be learned faster than HSS. A carbide turning tool is a popular choice for woodworkers who are not experienced. HSS turning tools produce curly, long shavings. Carbide tools can produce smaller shavings. Both of these materials can be used to fill holes in natural wooden stock. They also offer a higher cutting speed. If you are just beginning, a carbide cutter may be the right tool for you.
Skew
Most skew turners use a factory grind skew, which is often blunt. A good bevel angle is 25 degrees for softwoods, and 60-70 degrees for hardwoods. To save money, you could also make a skew using a HSS block. These tools are best for small items, such as pens, but they are also useful for larger items as well. In this article, we'll discuss some important tips for sharpening skews.
First, use a knife to cut beads. This tool should be held with the heel of the hand. During cutting, the heel must be in direct contact with the tool rest. You should get instruction and practice if woodturning is new to you. You can learn how to make a good skew by practicing. Below are some useful skew tools.
Adjustable sharpening jig
The purchase of a set does not mean you will have to spend time or money sharpening the tools. Many tools are already pre-sharpened. Some sellers also offer tools with interchangeable carbide inserts. Many skilled turners would not recommend purchasing these tools. They say traditional tools are more effective, provide better surface finishes on wood, and cost less in the long run.
Bench grinders are the best method to sharpen turning tools. This may work for older tools, but it will not replicate a sharpened one. It takes practice and a strong hand to use a bench grinder. Reshaping a piece wood can be time-consuming and difficult. It is difficult to reproduce the shape or sharpness of an existing tool using a bench grinder. This can lead to a dull tool. A bench grinder can make it difficult to replicate the shape and position of an existing tool. An adjustable sharpening knife jig will help you achieve a perfectly-edged tool every time.
CBN grinding machines
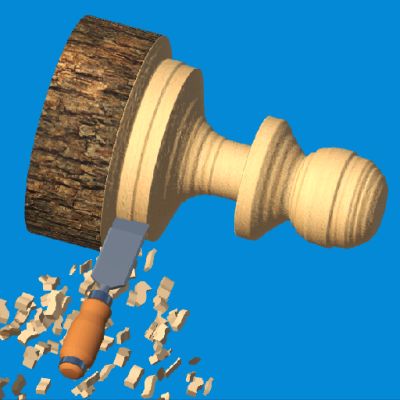
CBN wheels for turning tools offer several benefits, including increased strength and durability. These grinding wheels come in a variety of sizes to suit different spindles, and can be ordered in 150mm, 200mm, or 250mm diameters. These grinding wheels are available in different diameters. Most have a 40 mm width and a 32mm hole. Some models require shims that can be adjusted to the spindle's size.
CBN wheels are extremely durable, compact, and sharpen turners tools. They can also be used to cut carbide. They are strong and durable due to the bond between the grain and the hub. CBN wheels are not made of soft metals. These metals can cause clogging and reduce their grinding power. These materials may limit the life of CBN grinding wheels, so use them responsibly. Unless you use these tools for ferrous metals, you should avoid grinding them on soft materials.
FAQ
How much money does a hobbyist have to put into getting started?
A lot of capital is required to purchase the necessary supplies and tools if you want to start your own woodworking shop. You can start by purchasing a small table saw and drill press as well as a circular saw, circular saw, jigsaw and sanding machines. These items aren't very expensive, so you won't break the bank.
How often should I buy new supplies?
Some tools will need to be replaced over time. If you are using hand tools, you will need to sharpen them frequently. You'll also need to replace parts if you use power tools. Spread your purchases over several months to avoid purchasing too many items at once.
What's the difference between a hobbyist and a professional woodworker?
Hobbyists are passionate about making things from wood, while professionals tend to be more focused on the quality and craftsmanship of their work. Hobbyists often take pride in the creations they make and often share them to family and friends. Professionals will spend hours looking at designs before they start to build a project. They will meticulously plan every detail of their work from choosing the right materials to finishing it.
Which wooden items are very popular?
These wooden products are the most popular. They were made from sustainably harvested wood.
The most popular types of wood for furniture include oak, maple, cherry, mahogany, walnut, and teak.
These woods are strong and durable, with beautiful grain patterns. If they are well cared for, they can last many years.
Wooden furniture should always be painted first to protect against moisture damage. This applies to all surfaces, even drawers and doors.
A paint that resists water is the best choice to ensure that furniture lasts a long time.
A high-quality oil-based primer should be used, followed by two coats with top coat. Depending on the amount of wear, you may need several coats.
Spray cans or aerosol paints should be avoided. These products can evaporate quickly and emit harmful fumes.
Which material would you recommend for woodworking lessons?
Start with softwoods, such as pine or poplar. You will feel more comfortable with these softwoods, so you can move onto hardwood.
Statistics
- Most woodworkers agree that lumber moisture needs to be under 10% for building furniture. (woodandshop.com)
- In 2014, there were just over 237,000 jobs for all woodworkers, with other wood product manufacturing employing 23 percent; wood kitchen cabinets and countertop manufacturing employing 21 percent. (theartcareerproject.com)
- Overall employment of woodworkers is projected to grow 8 percent from 2020 to 2030, about as fast as the average for all occupations. (bls.gov)
- Average lumber prices rose about 600 percent between April 2020 and May 2021. (familyhandyman.com)
External Links
How To
How to stain hardwood
Staining wood refers to applying chemicals to wood's surface. This chemical reaction causes the wood to change in color. This chemical reaction causes the wood color to change from white and brownish red. While oak is the most widely used type of wood for staining purposes, other types of wood are also available.
You can apply wood stains in many different ways. One method involves mixing the stain and a solvent and then spraying it on the wood. Other methods use a solution of water and dye applied directly to the wood. You can also mix stains with varnishes or paints so that they become part the finish coating.
Preparing the surface for staining wood is the first step. Cleaning the wood thoroughly removes any dirt or grease that could interfere with applying the stain. Sanding the wood smooths out rough spots and scratches. The next step is to determine the type of stain you would like to use. There are two main kinds of stains available: non-penetrating stains and penetrating. Penetrating stains penetrate deeper into the wood than non-penetrating ones, making them ideal for dark colors such as mahogany. Non-penetrating stains work best with light colors like maple.
You will need to decide on the type of stain you want to use, and then prepare your tools. A paintbrush works well for applying stains because it allows you to spread the liquid evenly across the surface. It is a good idea to have rags on hand in case you need them to clean up any stains that may remain after you have finished painting. If you plan on mixing the stain yourself make sure that you have enough containers to hold the different components.
After you have prepared the materials, you can clean the area where you want to stain the wood. Use soap and warm water to remove dust and grime. Wipe down all furniture pieces with a dampened cloth and clean water. Take care to remove all debris and dirt, especially if you are planning on staining darker wood.
The stain should be applied next. Start at one end of the piece of furniture and brush or spray the stain onto the wood. Work slowly and carefully, moving back and forth along the grain of the wood until you reach the opposite end. Keep the stain from dripping off the wood's surface. Before proceeding to the next step, let the stain dry thoroughly.
To protect the painted surface, apply a coat of clear polyurethane sealant. Three coats are recommended for polyurethane. Let the third coat dry overnight before you sand the final coat.