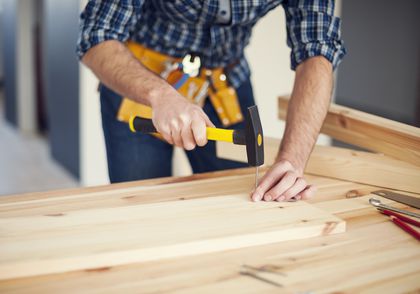
Cutting rough lumber can be tricky to load into your car. Bring your tape measure, hand saw and saw to the hardware store. In case your board does not fit, you can purchase additional boards. It is important to ensure the board you buy has knots and checks. If they don't, it may not plane as smoothly as you had hoped. You don't want to have to rip a board and start all over. It will take time and cost you money. So, it is a good idea to buy a few extra boards.
Minimal wastage
A sawmill usually turns 59% of rough lumber into boards when cutting it. The remainder of the log can be considered waste, including sawdust, bark, chips and chips. A less-than-perfect cut results in more waste, but it should still be less than 20%. Here's an easy formula to calculate how much wood is left over after a board has been cut. For a nominal 4-foot board, the sawmill should remove about 18% of its volume to achieve the desired lumber thickness and width.
For one, rough lumber doesn't come in uniform sizes. You can plan your project around the dimensions of hardwood purchased at big-box stores. The rough edges of lumber can be uneven, which leads to wasted material. Furthermore, rough-cut lumber usually requires a common width, which causes a lot of wasted lumber. This waste cannot be reused later.
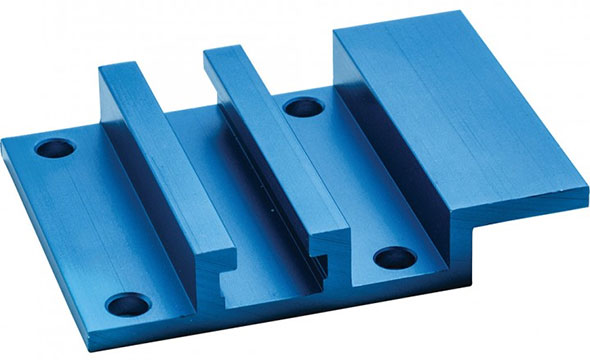
Preparation
Measure the length of your material before you start cutting rough lumber. The lumber yard may not have the rough lumber perfectly flat upon arrival. It may not be perfectly flat and have uneven edges and faces. Therefore, it may take multiple passes to flatten. It is a good rule of thumb to take out 1/16" per pass. If your lumber has concave surfaces you should run it through the saw keeping the concave surface in place.
It is recommended that rough-cut lumber be flattened until it is 1/4 inch thick before being cut. After flattening and sanding the face, plane it to the thickness of your finished board. Measure the length and width of the finished lumber once you have determined the thickness. You should account for any imperfections. You should leave about a quarter inch between the boards. Then, plan your project around the available boards. It is important to ensure that the lumber you purchase is flat. Unfinished boards can be difficult to work with.
Cost
There are two types. Dimensional lumber and rough-sawn. Home improvement stores usually carry finished lumber, but not often rough-sawn lumber. Lumber yards and local sawmills tend to carry both types of lumber. The only difference between these two types lies in the work involved. The cost of rough-sawn lumber is lower because it needs less processing. It is also more flexible than finished lumber in that it can be cut wider and thinner.
While buying lumber from a yard or mill is cheaper, you are less likely than others to find it in standard lengths. Milling your own lumber can be a cost-effective alternative to buying rough-sawn lumber, though you'll need shop space and upgraded power. Milling equipment can be noisy and requires training. Zoning laws may be necessary if your mill is to be used in an area.
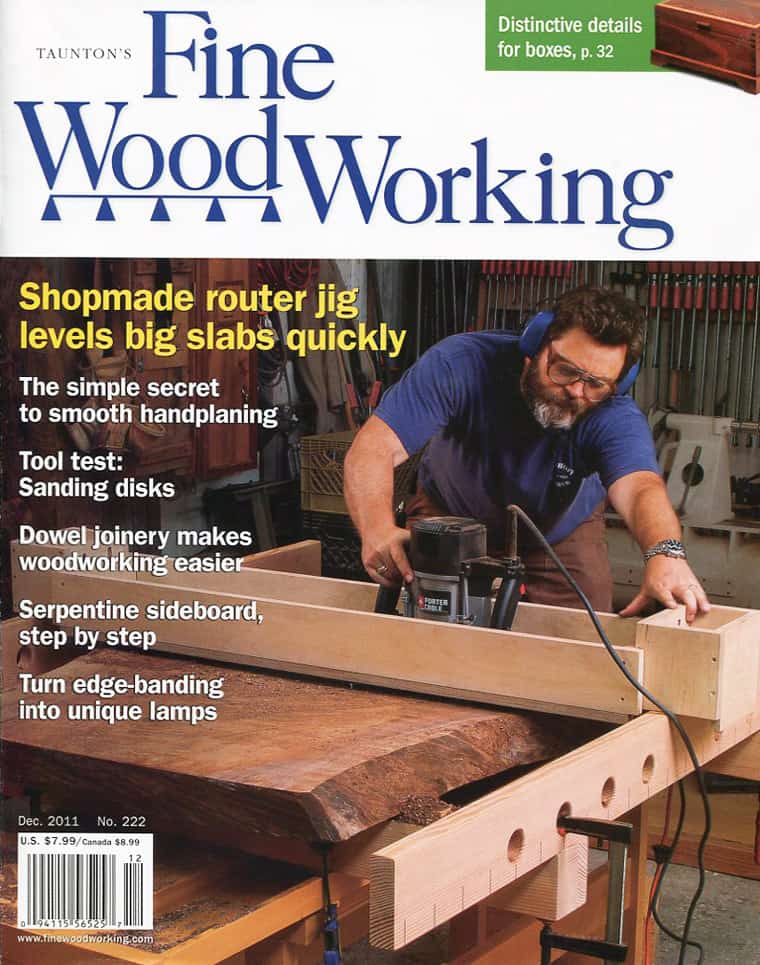
Source
There are many options for lumber purchases. There are many sizes and shapes to choose from, as well as different finishes. Rough sawn lumber can be described as unfinished and unsanded lumber that is not cut into planks. This lumber is stronger than the other types due to its higher moisture content. However, it is thicker than standard surfaced wood. These are some of many advantages to rough sawn lumber in your woodworking projects.
The first pro is its low cost and availability. Rough lumber does not need to be treated and cannot usually be purchased at a hardware shop. However, this type of lumber has its pros and cons. It's cheaper by volume but more expensive per board foot to haul. Plus, it takes more time to finish than treated wood. You might also consider this option when deciding how much lumber you should purchase. If you plan on using rough sawn lumber for your project, consider purchasing a large quantity of it and a small amount for finishing.
FAQ
What's the difference?
Hobbyists enjoy creating things out of wood. Professionals tend to focus on the quality. Hobbyists take great pride in their creations, and share them with family and friends. Professionals will spend hours researching designs before they begin working on a project. Professionals will be meticulous about all aspects of their work, from selecting the right materials to finishing it.
Do I have the potential to make a decent living doing this?
Yes! In fact, many woodworkers already do. According to U.S. Bureau of Labor Statistics (BLS), woodworkers earned a median annual salary of $34,000 in May 2012. This is significantly higher than the national average, which is $31,000 per year.
What tools do I need to start as a woodworker and what should I learn?
Woodworking takes practice and patience. Learning how to use the various tools and techniques necessary for woodworking takes patience.
There are many different types of woodworking equipment available on the market today. Some prefer to use power tools, while others prefer to use hand tools.
While you have the option to pick what you like, it is essential that you get the right tool for the job. It may be a good idea to start with a basic set, if possible, if you don’t know much about hand tools.
You might also want to learn how a router works, which allows you to cut wood into intricate shapes. These routers can be purchased at most hardware and home improvement stores.
Statistics
- Average lumber prices rose about 600 percent between April 2020 and May 2021. (familyhandyman.com)
- Overall employment of woodworkers is projected to grow 8 percent from 2020 to 2030, about as fast as the average for all occupations. (bls.gov)
- Woodworkers on the lower end of that spectrum, the bottom 10% to be exact, make roughly $24,000 a year, while the top 10% makes $108,000. (zippia.com)
- If your lumber isn't as dry as you would like when you purchase it (over 22% in Glen Huey's opinion…probably over 10-15% in my opinion), then it's a good idea to let it acclimate to your workshop for a couple of weeks. (woodandshop.com)
External Links
How To
How to make wood joint
This tutorial will teach you how to join two pieces wood together. We'll use the "pocket hole joint," which means we drill holes in the wood and then glue them together. This method is great if your wood's straight and smooth. You may want to consider other methods, such as dowel joining. These are the steps
-
Drill Pocket Hole Joints. You will need to measure and mark the exact location of your pocket hole joint. With a handheld drill machine or jig saw, drill 3/4-inch deep holes in the ends of each piece.
-
Sand Smooth. The wood's edges can be sanded to prevent splitting.
-
Glue Together Apply glue to both ends of the wood. Let the wood sit for 5 minutes, then clamp it together.
-
Fix the Pieces together. After the glue has dried completely, you can clamp the pieces together until they are flush.
-
Trim Joinery. Trim any excess wood surrounding the joint once the glue has dried completely.
Make sure to leave enough room between the pieces so that you can turn them inside and out.