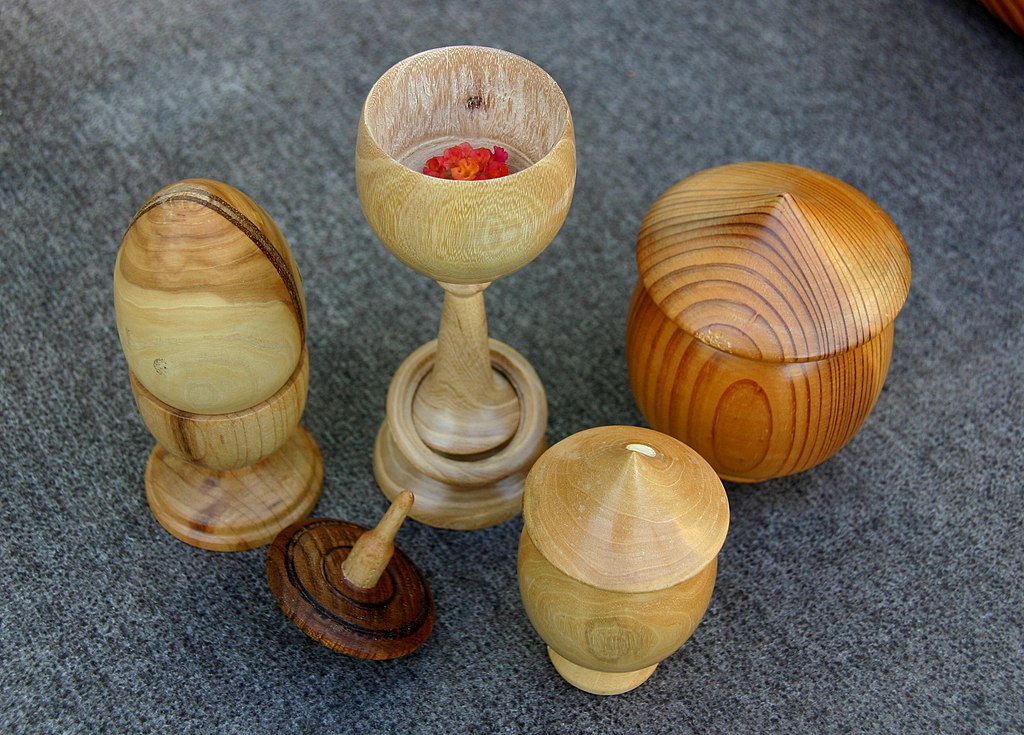
If a lathe doesn't have a suitable tool rest, you might need to adjust the angle on the top bar to correct for your awkward finger placement. Most tool rests have flat spots on the top bar that allow your fingers and thumbs to move back and forth. Some are adjustable, and can fit most lathes. While others have multiple height settings. Consider these important features when shopping for a toolrest for your lathe.
Light source
If you're not familiar with the concept of a light source for a tool rest for a lathe, you're not alone. Many lathes come with overhead lighting as well as fixtures that attach to the ceiling or headstock. These lights offer additional lighting, but can block operator access. For larger lathes, a tool rest with an integrated light source is the best option.
A tool rest for lathes includes a horizontal arm and a vertical post. The tool arm has a light source on its front, which is usually an LED illumination strip. The strip is attached to an electrical power source by means of a wire 20. Alternatively, a tool rest without a light source is provided. This invention allows for the creation a tool rest that is more ergonomic and includes a light source.
Support element
Support element for toolrest for lathe eliminates unexpected movement problems. In the prior art, the toolrest is supported by a point-to-point abutting arrangement. The toolrest must support torque and axial force when tooling. Therefore, the friction force generated cannot be used to support the rest. This design poses safety risks. With the Support element for tool rest for lathe, the toolrest is stationarily supported against axial force and torque generated during tooling.
A toolrest is a piece of metal that stands on its own. The bar is used to provide restraint. It may also have grooves for positioning the tool. Some models have a handle to guide the tool while turning. These toolrests are made of either metal or wooden. Wooden toolrests should be smoothed. You can choose to have a wood toolrest if you do not have a budget for the support element.
Adaptive device
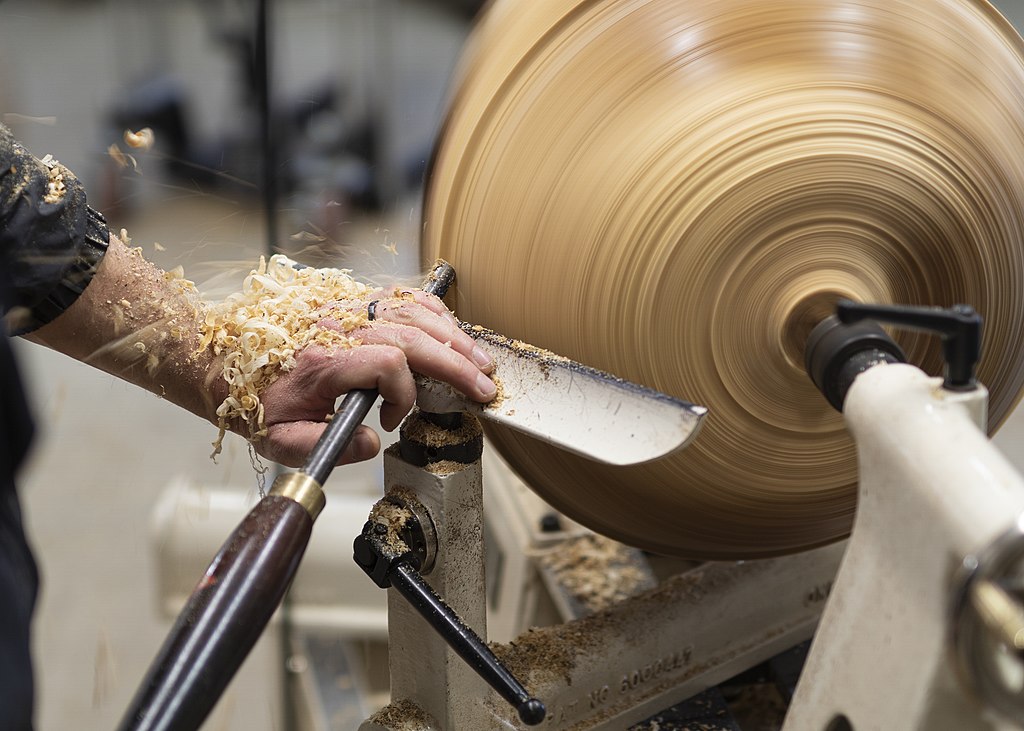
The adaptive device 100 is an externally cylindrical sleeve with a head and threaded section. There's also a threaded portion on the outer edge that connects to an opening 150. A flat surface 160 is formed by the milled shoulder 140 to accept set screws in the latheholder 310. The set screw 370 is pressed against the flat side 160 to secure the adaptive device within the lathe.
Although the Mortimer pin rest claims to have a gated function but the support bar rides almost parallel to the tool shaft so it should be able provide enough levering power sideways. This device has a very large gate, which almost certainly suffers cam locking. This is a significant improvement on a standard tool rest but it does not offer much in the way of motion restriction or fine tool control. It is not a good choice for those who need complete tool control without sacrificing precision.
Cutting tool
You should consider purchasing a cutting tool support for your lathe if you are just starting out in lathe work. This accessory allows you to hold your tool as close to wood as possible during its rotation. The toolrest's body slopes backwards from the forward edge. This allows you to position your cutting tool at an optimal angle for efficient cutting. With a file, you can finish the surface of the cutting tool rest to ensure a smooth working surface.
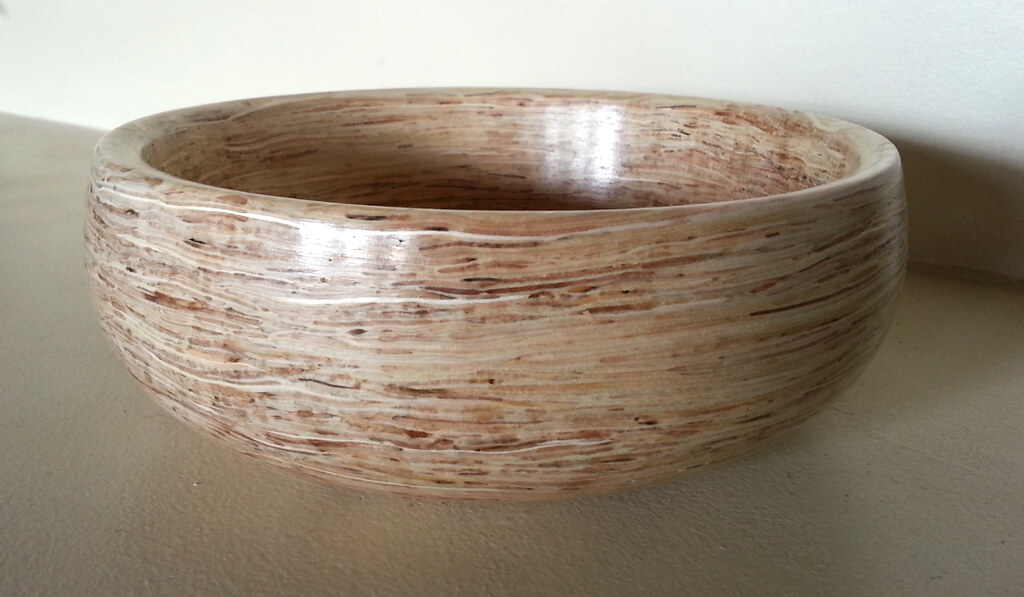
When purchasing a cutting tool rest for your lathe, look for one that has flat spots so that your fingers won't rub against the surface. This tool rest prevents your hands from sliding off the cutting instrument. It is also useful for keeping the workpiece stable during high-speed turning. There are many sizes available to fit your lathe. If you are unsure, ask a professional to help you make a selection.
FAQ
How can I tell what kind of wood I am working with?
Always check the label before purchasing wood. The label should include information about the wood species and its moisture content as well as whether or not it has been treated using preservatives.
Are there any other things I should know regarding woodworking?
Furniture making is a laborious task. It's easy not to appreciate how hard it is. Finding the right wood for the project is the hardest part. It can be hard to choose from the many types of wood that are available.
A problem is that wood doesn't have the same properties. Wooden can split or crack, while some woods may warp. These factors should be taken into account before buying wood.
How long does it take to finish a piece of furniture?
It depends on the type and complexity of your design as well as the amount of finishing that you use. Hardwoods, for example, require more maintenance than softwoods. Hardwoods are also more expensive than softwoods. They last longer and are more resistant to moisture. It takes between one and three months to finish a piece.
What would you recommend as a starting material for woodworking?
Start off with softwood like pine and poplar. These two are the easiest to master, then you can transition to hardwood.
What should a woodworker be paid per hour?
The hourly rate for a professional woodworker varies depending on many factors, including skill level, experience, availability, location, and other variables.
A skilled woodworker can expect an hourly rate of $20-50.
A less skilled woodworker can charge as low at $10 an hour.
Where can I purchase woodworking supplies
There are many places where you will find everything that you need. For example, you could visit local hardware stores or look online at websites like Amazon.com.
You can also look for used furniture at flea markets or garage sales.
Statistics
- Average lumber prices rose about 600 percent between April 2020 and May 2021. (familyhandyman.com)
- The best-paid 10 percent make $76,000, while the lowest-paid 10 percent make $34,000. (zippia.com)
- In 2014, there were just over 237,000 jobs for all woodworkers, with other wood product manufacturing employing 23 percent; wood kitchen cabinets and countertop manufacturing employing 21 percent. (theartcareerproject.com)
- Most woodworkers agree that lumber moisture needs to be under 10% for building furniture. (woodandshop.com)
External Links
How To
How to join two pieces of wood together without nails
Many people love woodworking. It's fun and relaxing because you can use your hands to make something useful from wood. You might want to join two pieces from the same wood, but you don't need to use nails. This article will demonstrate how to do so to preserve the beauty of your woodwork.
The first thing you'll need to do is cut off any rough edges from your pieces of wood before joining them together. Do not leave any sharp corners as they could cause problems down in the future. After you have completed this step, you are ready to glue your boards together.
You should only glue one side of hardwood. If you're using softwoods like pine or cedar, you should put glue on both sides. Once the glue has dried, press the boards together until they are fully adhered. After applying the glue, let dry the boards before proceeding to the next stage.
After you have glued the boards together, drill holes in the joints where you intend to place screws. You can choose the type of screw to determine the size of your holes. If you plan to use a 1/2 inch wood screw, drill a hole at least 3/4 inches in depth.
Once you have drilled your holes you will need to drive the screws through each joint and into the backside. Avoid hitting the board's top surface. Otherwise, you could ruin the finish. When driving the screws, try to avoid hitting the ends of the screws too much. This will prevent splitting in the end grain of the wood.
Once your project is complete, it's time to protect it against the elements. You can either seal the entire piece of furniture or cover the top. You want it to last years, so you can use any product. There are many options: oil-based varnishes; polyurethane; shellac; lacquer.
These products can usually be found at any home improvement store. Just make sure that you buy the right kind for the job. Don't forget to keep in mind that some finishes are toxic. Always wear protective gear when handling any of these finishes.